Parlor efficiency and productivity up on California dairy thanks to Cattle Care technology
Overseeing 45 total employees and milking 5,000 cows three times a day, farmer EJ de Jong of Hanford, Calif., knows first-hand the importance of an efficient parlor. As a forward-thinking dairyman, his curiosity sparked when first learning about Cattle Care's innovative video analytics for parlor management.
.webp)
Using a series of installed cameras, (which can simply be any pre-existing cameras on the farm) Cattle Care is able to visualize everything happening in a parlor – equipment, milkers and cattle. It then generates an automated report about all established protocol deviations that occurred during a particular shift. Its software also tracks progress, reports errors and specific incidents so that the manager can address them effectively and incentivize preferred behaviors.
"It has been very eye-opening and very helpful to actually know what's going on in the barn" de Jong shares.
A new way or parlor management
Overall, de Jong says that working with Cattle Care helped them lower their somatic cell counts. Additionally, their milking shift time frames are much more consistent than they ever were before.
One of the most significant changes the software helped de Jong make was implementing an incentive system that offers bonuses to employees according to shift once meeting a set minimum criterion.
.png)
"For better criteria, then they'll get a little better of a bonus," de Jong explained. "When they hit our optimal goal, then the bonus is pretty hefty."
The system, he adds, has helped express the need for better employee communication.
Another thing de Jong did was create a new position for a milker manager. This person was promoted and designated to observe the system’s analytics and talk to employees on shifts consistently flagged for specific errors.
"One thing that they improved right away was the percentage of cows that were not getting post dipped," says de Jong.
When starting with Cattle Care, he saw that only about 90% of the cows were getting properly post dipped after milking. After identifying the problem and addressing it with employees, he said that number almost immediately shot up to virtually 100%.
Another thing they found to improve was manually detaching cows too soon. While their parlor has an automatic vacuum shutoff based on milk flow, it used not to be uncommon for impatient human nature to lead workers to manually detach milkers too early.
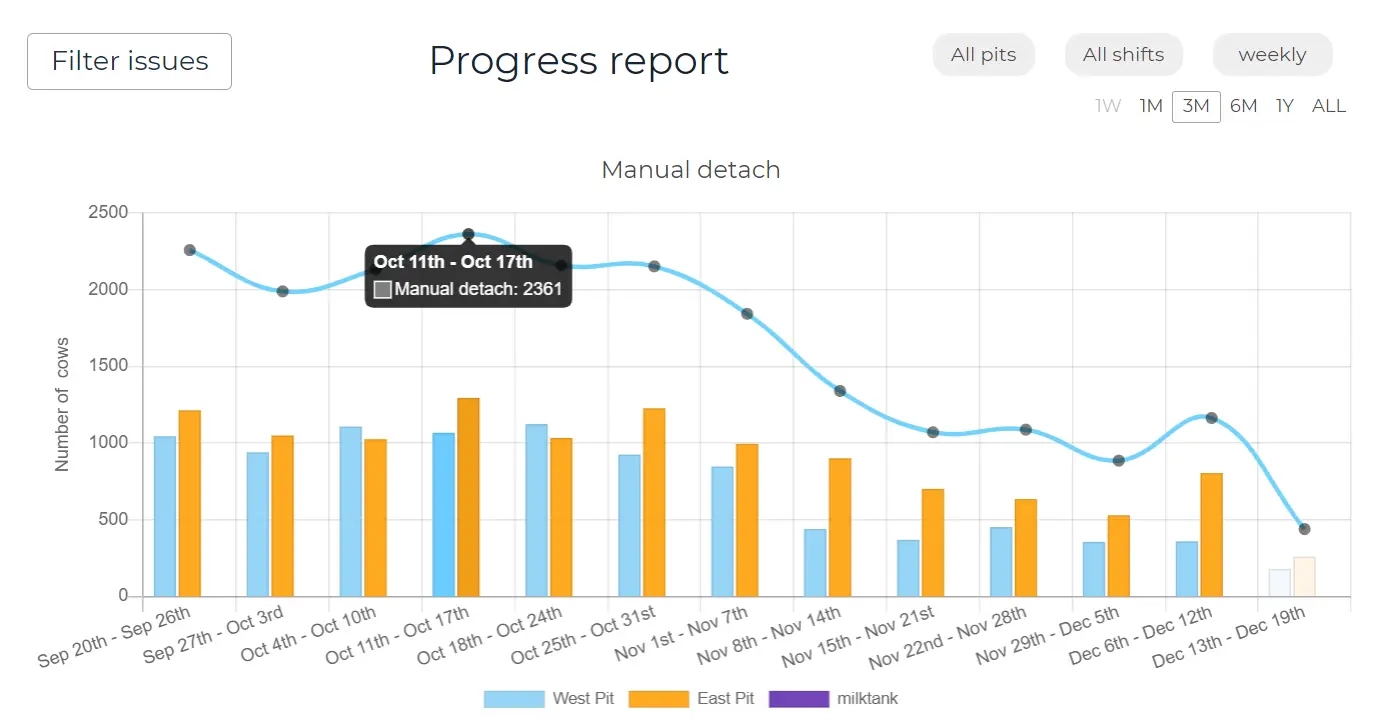
"We've been able to reduce that quite a bit," said de Jong. "It'll probably never be 100% because you can't have 40 cows waiting for one; you're always going to have a percentage (of cows) that are really slow milkers. Those ones we have to detach, but we're getting comfortable levels with that number."
On the flipside, Cattle Care is also helping them catch times when machines come off too early. In some cases, employees might assume the cow is finished milking without checking her udder for assurance.
"In those cases, we're measuring those as well," says de Jong. "Protocol is you got to catch it within 45 seconds… there's a percentage that they don't catch. (Now) we're flagging that and working on it."
These positive changes were made possible under the analysis of Cattle Care with behind-the-scenes decision-making by de Jong and his team. Doing that required a bit of a learning curve.
Working with the system
Learning about issues in the parlor with statistical analysis and management is notably different from arbitrarily reviewing a video or making "guesstimates" based on time.
"It makes you look at things from a completely different perspective," says de Jong. "It's a totally new way of looking at (parlor management)."
Something that helped him in the early stages was the Cattle Care team. Every two weeks, they would hold Zoom meetings with de Jong. Together they would discuss trends they were seeing and brainstorm ideas that would have positive impacts. They also evaluated what progress their changes were making.
"There are certain things you got to prioritize; you got to pick your battles," he says. "It's great technology and catches a lot. But at the same time, we can't be running this place like the Gestapo."
He notes that, especially with the difficulties in finding reliable labor, handling employee issues is critical.
Employee improvement
Something that has helped de Jong immensely at tackling problems is the alerting Cattle Care does to issues in the barn. Otherwise, he says it would take hours manually going through video footage to identify problematic behaviors, then even more time to evaluate them and then address them directly to employees across three different shifts.
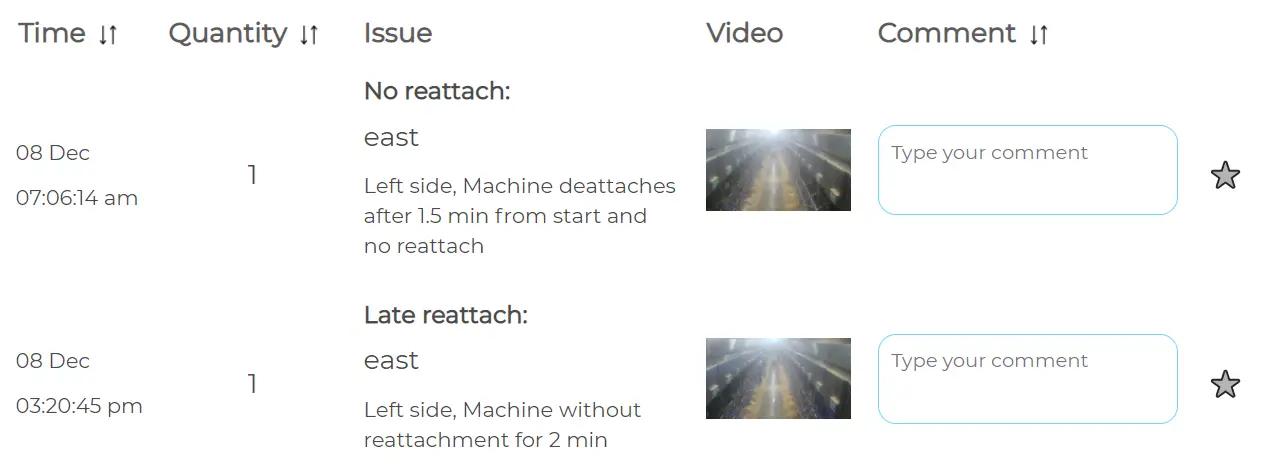
The advanced Cattle Care algorithms not only accounts for what the issues are; they also take the data and visualize it. This way, EJ and his team can physically see the procedural drifts and differentiation in a working progress report of charts and graphs. The report can be customized to differentiate between shifts and procedures. Each time data is collected, it can be compared against past performances to see improvement or regression.
With a concrete way to measure and reward proper milking parlor protocols, the difference in improvement is paramount. De Jong believes this is much more powerful compared to just verbally making corrections.
"With the implementation of the bonus program (employees) have total control whether or not their shift gets it because they know what metrics," he says. "Looking at the first series that we did, we saw a pretty dramatic increase once we offered the incentive."
Continual success
Overall, de Jong says he is impressed with the aid of Cattle Care and the quality in working with their team and continual development.
"(Cattle Care's) responsiveness to ideas and the speed that they come back with solutions in the software or the interface has been really impressive," he says. "I think they're just going to be constantly improving and constantly developing. It's a really good product now and it's going to get better."
Please reach out if you're interested to learn more - Contact Us!
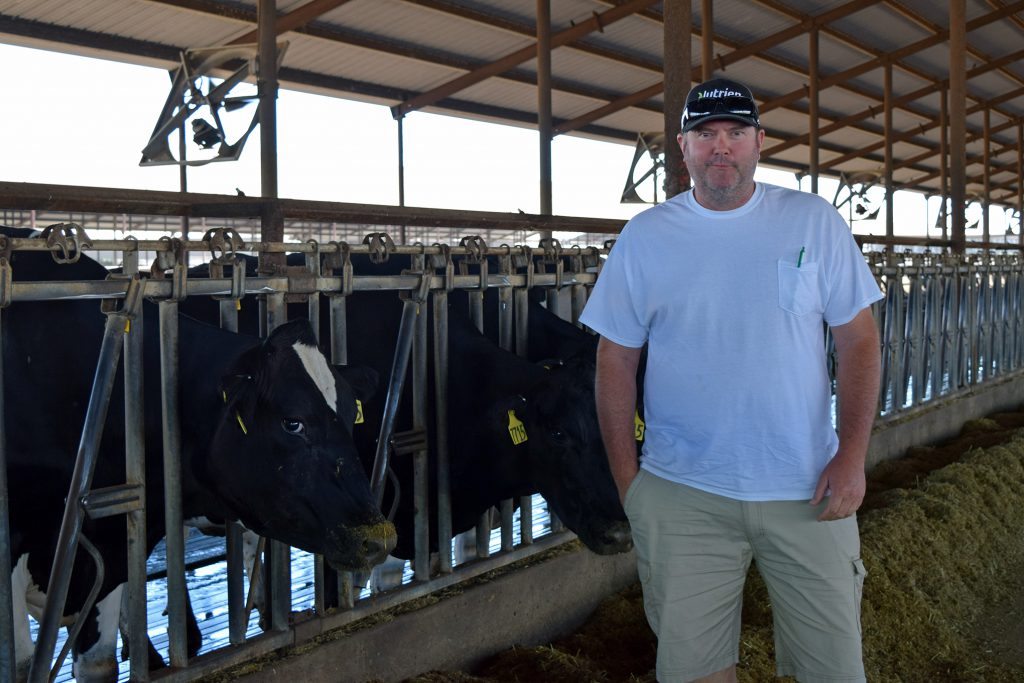